13 common problems when slitting and cutting blown film, and what you can do about them
Troubleshooting Common Slitting and Cutting Problems for flexible packaging manufactures
Blades are needed for converting blown film into desired dimensions. This text focuses on common problems and their solutions when cutting or slitting blown film. It will go through 13 common problems for flexible packaging manufacturers. It also describes the most common parameter adjustments operators can do to avoid problems and optimize production.
Download PDF with Sollex Blades for Plastic Industry
The main reasons for slitting and cutting problems are blunt or improperly sharpened knives. Sharper knives provide greater efficiency when cutting any material. Sharper knives produce a cleaner cut without tearing, resulting in greater efficiency, higher throughput, and a better quality end product.
About problems encountered when slitting and converting blown film containing many additives and mineral-based fillers, and how to solve them, you can read in a dedicated article"7 Challenges in Slitting Blown Film with Filler Masterbatches".
Content:
- Interrupted slit
- Inferior cutting edge quality
- Short blade service
- Short blade service - optimize your settings
- Dust formation
- Teared plastic film
- No roll separation and material jam in front of slitting
- Rough roll edge - Non straight edge - Annual growth rings
- Non straight section line and Filament building / "Angel hair”
- Edge build-up during winding
- Blade edge shows burrs and dents
- Chips on the cutting edge after grinding
- Wrong handling, packaging, and storage of knives and blades
- Sollex blade recommendations for high speed blown film machines
1. Interrupted slit
Interrupted slits are extremely important to avoid when producing blown film and foil. Interrupted cuts are usually caused by damaged blades or an incorrect cutting angle. Bottom knife runout or low lateral contact pressure can also result in interrupted slits. Professional blade sharpening is a repetitive process in which quantity and quality go hand in hand. A larger quantity usually leads to better quality. So buy and resharpen your machine blades in batches, and you're more likely to get more consistent quality.
2. Inferior cutting edge quality
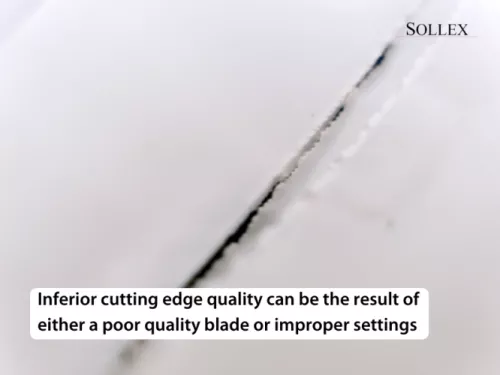
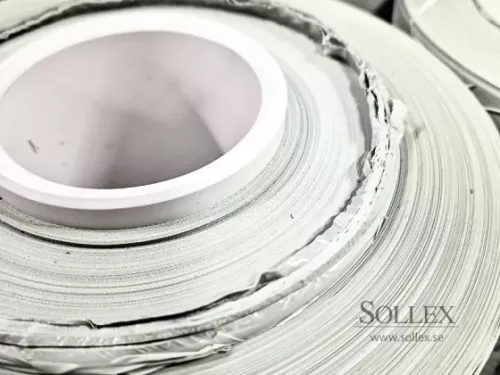
Inferior cutting edge quality can be the result of poor blade quality or improper settings during the cutting process. A blunt or burred blade alternately a blade with poor grinding will result in inferior cutting edges. Other reasons can be offset knives, blade vibrations, or wrong web guidance. Too high lateral contact pressure or the wrong shear angle are also reasons for worsened cutting edges.
Therefore, if you notice a deterioration in the quality of the cutting edge, start by replacing the blades. If the quality of the cutting edge has improved, you can choose a blade with better characteristics (e.g. with a different coating or made of a different material). If blade vibration is the cause, try using a slightly thicker blade or knife. Changing the blade from 0.13mm to 0.20mm can significantly affect blade vibration, although in general you should try to use as thin a blade as possible. Vibrations alter the cutting angle. Blade and equipment vibrations should therefore be avoided.
3. Short blade service - test other blades
Steel is a relatively soft material that will not stand long-term abrasive wear. Poor steel gives short durability as the blade edge will wear down quickly. Many factors influence abrasive wear and how blade material is removed. Fragments of the blade edge are separated, generating small fractures in the blade edge. Similar to grinding the film grit will wear down the blade edge. The more abrasive additives in the film, the faster the blade will be worn down.
Hard metal and ceramics are much harder than steel and can be used to protect the edge or make blades that withstand abrasive wear much better than steel. A Sollex customer converting process with a film containing white chalk showed how durable hard metal and ceramic coatings could be. A normal razor blade lasted 20 minutes. The same blade with Sollex ceramic coating lasted 2 weeks. Different web materials require different blades. However, it is possible to have blades with high performance and long durability.
Material changes give different abrasive wear on the blade. Different films wear the blade down in different ways. A laminated film with PP, PE, PET and additives such as Titan (TiN) wears down almost all blades. One Sollex customer had a problem with this film until he found 5V. A top-performing, hard metal, long-lasting slitter blade that endures abrasive wear. There is a correct blade for each purpose.
4. Short blade service - optimize your settings
Other reasons for short blade service can be too high lateral contact force or too large shear angle. Equipment vibrations can ruin the blade and be the root cause for short blade service.
For top and bottom knives, a too-large knife overlap or outrunning bottom knives will severely diminish the blade service lifetime. In addition, it is important that the axial speeds of the top knives to bottom knives are the same as the material web. Finally incorrect regrinded knives will also play games with the cutting quality and the knife lifetime. Read more about this topic in Slitting Methods to Cut Web Material: Shear, Crush and Razor Slitting blog post.
5. Dust formation
High-performance industrial razor blades provide a cleaner cut of web materials compared to top and bottom blades. Cleaner cuts reduce the presence of dust particles between film layers, resulting in an end product with higher quality.
Razor blades provide inferior slitting quality in blown plastic film production. Dust is the most unpleasant production factor for film manufacturers. Even if you use a razor blade, you can get dust. Each film is unique and requires a precise blade for cutting. For example, white film cut with an ordinary razor blade can produce dust, as demonstrated in this picture.
The picture shows a white film being cut at 250 m/min. But the same film being slit with a Sollex-K blade (ceramic-coated blade) produces almost no dust and can run in 350 m/min. We have found that dust generation with razor blades is related to blade thickness, topography, and blade edge friction.
When using circular top and bottom knives, blunt top knives or improperly sharpened top knives are most likely to cause dust formation. Parameters such as too much knife overlap or cutting angle should also be considered when minimizing dust. Finally, unstable blade guidance is a common factor in dust formation during cutting. Make sure that the blade guides are fixed and sturdy so that no dust is generated.
6. Teared plastic film
It is a relatively common problem for film manufacturers to tear film instead of cutting or slitting. Torn film gets useless, so avoiding tears is imperative for flexible packaging manufacturers. The material web line usually tears off at the point of intersection.
We find several reasons for tearing. For razor blades, tearing appears when the topography of the blade edge affects the web. A blade optimized for slitting film with white chalk may tear a thin, stretched film at high speed. Counterwise, a blade made for stretch film may be useless for slitting film containing white additives.
For top and bottom knives when shear slitting, teared film occurs when there is a knife offset for the top and bottom knives, which means they are wrongly adjusted for a tangential cut. An alternative is that the knife overlap is too large. Not strictly related to the slitting process but still a very common cause for tears is incorrect web guidance or that the exhaust waste strip needs to be adjusted.
7. No roll separation and material jam in front of slitting
One possible serious consequence of material tear can be the lack of roll separation. Basically, the material web does not separate because the tear glues the film back together due to electrostatic attraction.
Other reasons for the non-separation of the rolls could be that the listing tools are damaged or the web tension is too high. As always, in order to correctly separate rolls, the web should be guided or supported at the point of intersection. Material jamming in front of the slitting zone and roll separation can be the result of too slow feed of the bottom blade.
8. Rough roll edge - Non straight edge - Annual growth rings
Another consequence of tearing could be an uneven roll edge. Winding layer after layer of rough roll edge looks like absurd annual rings from a cut tree rather than a desired CD-disc. Again, blade edge friction and material type play an important role. Therefore, it is critical to have the right blades for the specific application. Annual rings when slitting stretch plastic film can also be created by inconsistent material tension or a loose shaft.
A rough edge of the roll, a non-straight edge, or the more common name for annual growth rings creates electrostatic stress between rolls of film. Placed together on the pallet, these tensions can act like glue, making it impossible for your customer to separate the rolls. As a result, your customer may complain about the quality or find the shipment useless.
9. Non straight section line and Filament building / "Angel hair”
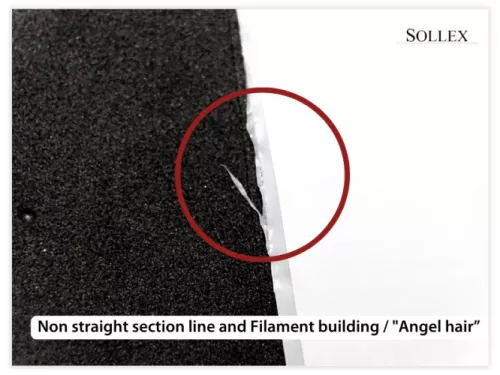
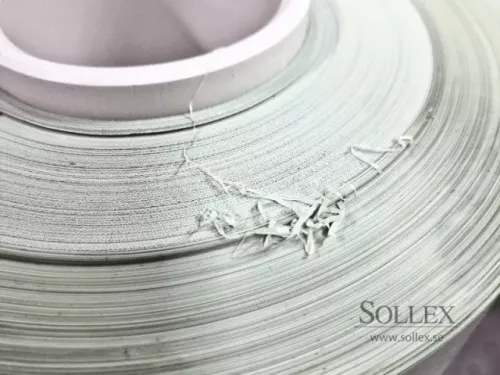
Non-straight section lines can occur when using top and bottom knives. Non-straight section lines are usually the result of loose knives or a worn-out bottom knife. Make sure the cutting equipment is properly fixed and the bottom knives are resharpened or new.
"Angel hairs" is a clear sign that the cutting process is not working properly. Look for vibrations and monitor the operation of the top and bottom knives. It may be time to replace or regrind. If this scenario happens often, you may want to consider a different blade design to make it work.
10. Edge build-up during winding
Optimized industrial razor blades produce clean cuts. Poor blades can cause corrugations on the material cut edge. When the web is winded, corrugations upon corrugations give a raised roll edge. This builds up the material edge. Edge-built-up films are often considered unusable as they possess large difficulties to unwind.
If you are experiencing edge buildup up when using top and bottom knives, it might make sense to try using razor blades instead. Since the top and bottom blades work at high cutting speeds, they produce poor-quality cuts. The cut with a razor blade will be cleaner.
If industrial razor blades create a buildup of edges on the web of material, it is recommended that you first check the direction of the web and make sure that the foil is slightly stretched against the cutting blade. Also, make sure that there is constant material tension and that the shafts are fixed. After checking the settings of the slitting process, the next step is to test the blades of different thicknesses. A general recommendation is to try thinner and thicker blades to look for improvements or deteriorations. For example, if you are using a 0.20mm razor blade, test how a 0.13mm or 0.30mm blade will affect your cutting and edge build-up. So, for thin stretch film at high speed, check 2-013-Z, 2-020-Z or 2-030-Z. For film containing white additives such as chalk, try 2-013-K, 2-020-K or 2-030-K. For thick multilayer films containing layers of Polypropylene (PP), Polyamide, and Elastomers (TPE) we have found that our blade 2-020-V works well to avoid Edge build-ups. Like-wise when it comes to adding colors 2-020-X works wells when slitting in printed areas and still minimizing edge build-ups-
Check which solution gives the lowest edge buildup - iterate from there.
11. Blade edge shows burrs and dents
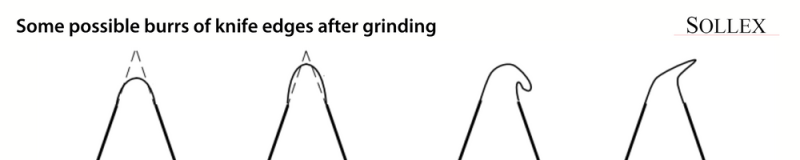
Burrs and dents are the worst proof of insufficient blade quality. Burrs and dents show that the blade manufacturing process is malfunctioning. Alternatively, the batch is useless. Burr is blade material (most likely steel but can be ceramics or hard metal) that has not been removed by the last and finest grinding of the blade. Dents are small cracks in the blade that imply that the blade has been damaged. With burrs and dents on the blade edge, it's time to change blades.
There is a very effective way to check blades for burrs and dents. Take two blades and slowly slide them edge to edge. You will feel burrs and dents directly. An alternative is to use light on the edge to see spatial differences.
12. Inferior regrinding quality - Chips on the cutting edge after grinding
Blunt slitting tools can cause the material web to penetrate between the top and bottom knives. Regrinding is therefore a serious and professional craft. For high-performance circular knives, you need a really good regrind and someone you trust. The optimal way is to let your original manufacturer regrind. Then you will have the most similar re-grinding as the original knife. When regrinding you will get new angles or shorter diameters. So blade design and performance will change. Wrong or bad grinding / regrinding can result in too low lateral control pressure. In addition, improper regrinding can result in chips, dents, and burrs on the cutting edge.
13. Wrong handling, packaging, and storage of knives and blades
Bad handling of sharp knives is probably just as tough on blades as when they are worn out. Therefore, packaging and storage are extremely important for long blade durability. Depending on the design, size, and quantity, there are many different packaging options for knives and blades. With proper handling and packaging, blades can be stored for a very long time.
A quality blade packaging should:
- Protect the user
- Protect the blade from being damaged
- Protect the blade from rust
The steel will all corrode. Since stainless steel is resistant to rust, it can still corrode over time. A blade has to be lubricated to prevent corrosion. Wrapping it in protective paper is the second step. Utilizing a vacuum is a third tactic to prevent oxygen from reaching the steel. Because cardboard absorbs moisture, it is the recommended material for second packing. Lastly, the inside is shielded by a wooden exterior box.
Maintain a regulated, low-humidity atmosphere in any spaces where blades are kept or utilized. Relative humidity should ideally be less than 50%. It is recommended to keep the temperature between 20 and 22°C (68 and 72°F).
Industrial blades from Sollex are always supplied well-oiled and vacuum-sealed.
You may learn about how to keep industrial knives and blades from corroding here.
Learn more about industrial knife materials in an article Overview of Materials for Industrial Machine Knives.
Sollex blade recommendation for high speed blown film machines
Sollex is your industrial blade manufacturer and supplier. We are based in Sweden, Europe and work solely with knives and blades. We have a wide product range with different industrial razor blades such as slitter blades, straight three hole blades, round 3 hole slitter blades, injector blades, industrial double edge razor blades. In addition, we keep a lot of machine knives in stock.
Try Sollex Zero Friction blades: Type Z for stretched thin films without additives. For film with additives, such as white pigments, try Type K blades. A basic TiN coating blade type T can be used in a wide selection of applications.
PP with additives (for instance, such as calcium carbonate, which makes it similar to rubber) is really tough on the blade. Cutting such film requires extreme performance and durability. Sollex V quality, such as 5V, can work in extreme cases. Normal PP without additives should work with Sollex K and Z blades. C blades stay sharper even longer as they are self-grinding. But the C quality is also a bit fragile. If you require something between V and K, Sollex X quality is a good choice.
Read our guide about product qualities and coatings here.
Our industrial-type razor blades are made of high quality stainless steel with different coatings on the edge or side of the blades. Sollex blades are available in solid tungsten carbide or ceramics. If you do not find the razor blade you are looking for, Sollex are able to manufacture industrial razor blades according to your drawing.
Download PDF with Sollex Slitter Blades for Plastic Industry
Contact Sollex and we'll be happy to help you with samples so you can test them on your production line. You are welcome to contact us at +4635-15 75-00 or at info@sollex.se if you have any questions regarding our industrial razor blades.
About the author Johan Falk is an expert on knives and blades and the CEO of Sollex. You can contact him directly on: 0046 708 744 786 or johan@sollex.se. For general sales questions drop an email to order@sollex.se or call us on 0046 35 15 75 00
_______
Sources:
1. Wikipedia
2. Dienes https://www.dienes.de/en/, Accessed the 2 January 2023
3. Fortis https://www.fortisblades.com/, Accessed the 2 January 2023
4. ROBERT HARRISON, WITTMANN INC., Eliminate Dust, Fines and Longs For Better Regrind Quality, https://www.ptonline.com/articles/eliminate-dust-fines-and-longs-for-better-regrind-quality, Accessed the 2 January 2023
5. What is a burr? https://scienceofsharp.com/2015/01/13/what-is-a-burr-part-2/, Accessed the 2 January 2023
6. Source (for all SEM pictures here) from the scienceofsharp web page https://scienceofsharp.com/, Accessed the 2 January 2023